Феномен шпильки. Инжиниринг как рычаг импортозамещения, Газета "Поиск"
У этого человека целый букет должностей, каждой из которых хватило бы для работы «под завязку». Алексей Иванович Боровков – проректор по перспективным проектам Санкт-Петербургского политехнического университета Петра Великого. Менеджер университетской программы «5 – 100». Профессор кафедры «Механика и процессы управления». Научный руководитель Института передовых производственных технологий. Наконец, руководитель университетского инжинирингового центра, который, по мнению министра промышленности торговли Дениса Мантурова, является эталонным.
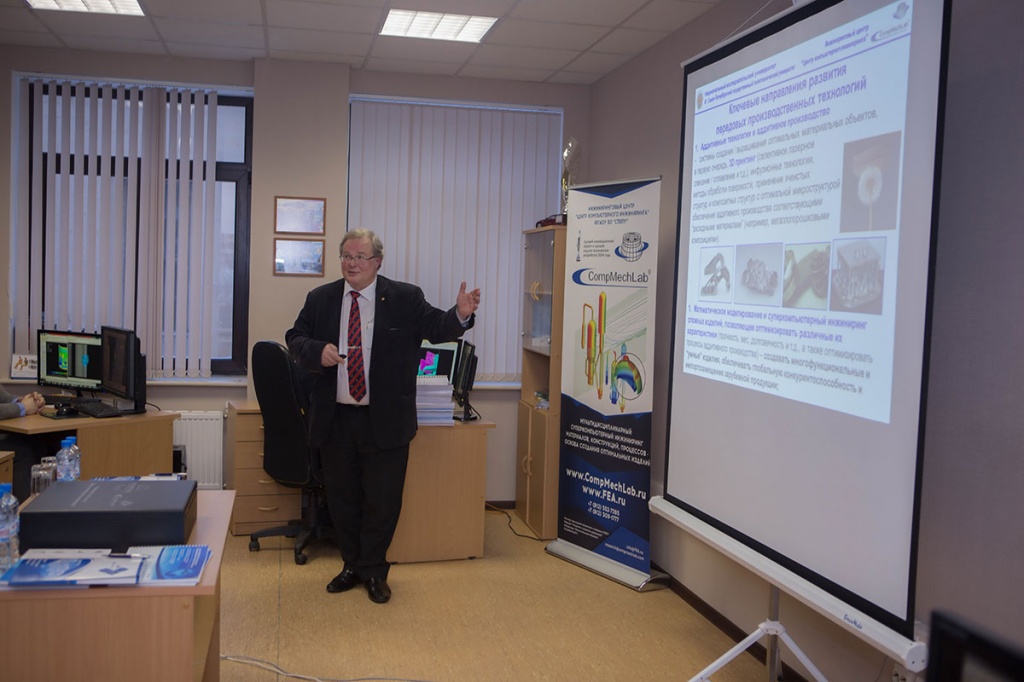
Признание непрофильного министра, согласитесь, дорогого стоит, при том что и «профильный» Дмитрий Ливанов высокого мнения об инжиниринговом центре Политехнического. Он занимает особое место среди созданных в рамках совместной программы Минпромторга и Минобрнауки вузовских инжиниринговых центров, поскольку оказывает услуги компаниям в различных отраслях промышленности – автопроме и авиапроме, машиностроении, судостроении, нефтегазовой отрасли… Универсальность определяется тем, что это единственный в стране центр КОМПЬЮТЕРНОГО инжиниринга, разрабатывающий и применяющий на практике полномасштабные мультидисциплинарные математические модели, адекватные реальным конструкциям и физико-механическим процессам.
Согласно неформальной характеристике, профессор Боровков – «специалист по нерешаемым задачам». Кто из российских инженеров разрабатывает линейку автомобилей премиум-класса с уникальными характеристиками для Президента России? Команда Боровкова. Кто способен, для примера, за несколько дней, фактически не имея исходных данных, оценить свойства материала, разработать рабочую конструкторскую документацию и изготовить импортозамещающую шпильку для морской ледостойкой стационарной платформы “Приразломная” – единственной платформы, ведущей добычу нефти на российском арктическом шельфе? Опять же сотрудники инжинирингового центра, разработавшие и применившие универсальный алгоритм реверсивного инжиниринга. Импортозамещение, убежден профессор Боровков, имеет смысл, только если выпускать продукт, конкурентоспособный на мировом рынке. А способность глобально конкурировать инжиниринговый центр Политеха доказал, сотрудничая с General Electric, General Motors, Boeing, BMW, Daimler, Schlumberger – не просто по отдельным проектам, а зачастую на регулярной основе, встроившись в их технологические цепочки. И, что ничуть не менее важно, на этом уровне, с учетом мировых трендов, осуществляет трансфер технологий мирового уровня, систематически выполняя НИОКР по заказам «Ростеха», «Росатома», Газпрома, Объединенных корпораций – авиастроительной, ракетно-космической, двигателестроительной, судостроительной, – компании “Силовые машины” и многих других высокотехнологичных предприятий российской промышленности.
Наверное, судьбе было угодно, чтобы этот кандидат наук еще советского розлива не ушел в конце 1980-х в кооператоры, а в начале 1990-х в продавцы компьютеров, подобно многим подававшим надежды ученым. Напротив, еще в 1987 году Боровков создал первую в стране лабораторию “Вычислительная механика” (CompMechLab), как с гордостью отмечает, на 10 лет раньше, чем аналогичная кафедра возникла в Московском государственном университете. Она-то и стала идейной, творческой и кадровой базой вузовского центра компьютерного инжиниринга. Попробуем разобраться, как удалось добиться соответствия результатов деятельности центра тем высоким целям, которые он декларирует: «в инжиниринговом центре мы должны иметь и эффективно применять все лучшие кросс-отраслевые технологии компьютерного инжиниринга мирового уровня, непрерывно совершенствуясь на каждом участке и этапе работы».
– Алексей Иванович, в том, что инжиниринговые центры страны и ваш в том числе оправдывают возлагавшиеся на них надежды, министры Мантуров и Ливанов убедились в январе этого года, посетив Политехнический университет. Тогда же говорилось, что центры эффективнее многих технопарков и бизнес-инкубаторов. А собственно, почему?
– Причина в том, что в программу создания инжиниринговых центров на базе ведущих технических университетов были изначально внесены очень правильные ключевые показатели эффективности. Помните, на совещании с участием двух министров, проходившем в питерском Политехе, говорилось, что первые 11 центров по итогам деятельности за год выполнили контрактов с промышленностью на 800 млн рублей, вдвое перекрыв объем первоначально предоставленных субсидий!
Если в развитие инжинирингового центра вложили миллион рублей, то уже за первый год своей деятельности центр должен выполнить реальных заказов от промышленности на сумму больше чем миллион рублей. Подчеркну – ЗАКАЗОВ ОТ ПРОМЫШЛЕННОСТИ. Именно такой сверхправильный подход совместно и своевременно применили два министерства. Другая очень правильная идея – отобранные в результате конкурса инжиниринговые центры должны быть лучшими в стране, причем университетам можно было заявить на конкурс лишь один инжиниринговый центр, но он должен быть глобально конкурентоспособным!
А потому не случайно, что даже в условиях секвестра госбюджетных субсидий, финансирование этой программы удвоилось, ради создания новых инжиниринговых центров и новых инновационных предприятий, в новых университетах и в других регионах. Поскольку в программе участвуют два министерства, то ее отчетные показатели характерны не только и не столько для Минобрнауки (количество публикаций и цитирований, диссертаций, участие в конференциях и т.д.), сколько для Минпромторга, а это – эффективное взаимодействие с промышленностью, в первую очередь, отечественной.
Иными словами, за бюджетные деньги ты не можешь отчитаться бюджетными деньгами (гранты и др.) и научными заделами – должен предъявить выполненные НИОКР по заказам реального сектора экономики. А если реальный сектор заказал работу, значит вложил свои деньги в решение актуальной для него проблемы, в этом главное отличие от инициативных грантов на научные исследования.
Как правило, промышленность заказывает работу и платит внешнему исполнителю деньги, которые могла бы потратить на себя, в двух случаях: когда сама не может создать конкурентоспособную продукцию или когда “маячит” упущенная выгода. Сотрудники нашего инжинирингового центра выполняли проекты, где неустойка из-за технических несоответствий или упущенная выгода составляли миллион долларов в день, что типично для атомной энергетики или нефтегазового сектора. Скажем, где-нибудь в Австралии нефтяная скважина «ослепла» на глубине нескольких километров. Сначала ее пробуют реанимировать, если не получается и вдруг «слепнет» вторая скважина – это уже серьезная упущенная выгода, и тогда обращаются к нам, чтобы разобраться с причиной.
– А если деньги принес зарубежный заказчик, это считается?
– Конечно, поскольку это означает экспорт высокотехнологичных инжиниринговых услуг, а если есть экспорт, то результаты нашей деятельности глобально конкурентоспособны. На одном из высоких совещаний мы предлагали ввести долю экспорта как один из ключевых критериев оценки деятельности предприятий, ведь это прямое признание мирового уровня конкурентоспособности. Нам возразили, что, мол, это преждевременно, «так можно обрушить российскую промышленность». Мне кажется, наоборот: только так ее можно стимулировать к поиску наукоемких инноваций.
– Сейчас промышленность готова платить за технологии, нацеленные на замещение импортной продукции. А вы готовы их предлагать?
– Когда программа развития инжиниринговых центров рождалась в конце 2013 года, понятия «импортозамещение» на слуху еще не было. Однако вскоре эта проблема стала актуальной и породила своеобразный феномен – стоит объявить о потребности в импортозамещении, как полстраны откликается: «это по нашей части, только дайте нам денег». Мы предложили провести конкурсный отбор, вроде того, что сами лет 10 назад проходили за право участвовать на постоянной основе в работах для лидера мирового автопрома – BMW. Соревновались полсотни команд со всего мира по системе плей-офф: тебе дается две недели, чтобы выполнить задание, эксперты оценивают результат, показавшие худшие результаты выбывают. Мы преодолевали этап за этапом. Затем состоялись визиты их технических специалистов и топ-менеджеров – для оценки инфраструктуры, кадров, организации процесса. Финальная стадия конкурсного отбора проходила в Германии, в штаб-квартире EDAG – Engineering + Design AG, крупнейшей (7 500 сотрудников) инжиниринговой компании в автомобилестроении. Две команды, мы и конкуренты примерно в течение пяти часов выступали на заданные темы, отвечали на вопросы технических специалистов и менеджеров. В результате победы в конкурсе наша команда получила эксклюзивный статус “Master Supplier” и за несколько лет вышла на режим совместной по схеме “365x24”.
Это взаимодействие развивается, у нас есть офис в Мюнхене, потому что телефонная связь, скайпы, электронная почта не заменят ежедневных личных контактов с инженерами, конструкторами и технологами компании-заказчика.
– Еще одно условие Минпромторга и Минобрнауки состояло в том, что каждый университетский инжиниринговый центр выводит на рынок стартап-компанию, которая тоже должна эффективно работать с промышленностью. Так?
– Совершенно верно, сотрудники университетского инжинирингового центра в первый же год своей деятельности должны создать малое инновационное предприятие (МИП), которое тоже должно стать лучшим! Мы вышли на конкурс с созданным годом ранее МИП «Политех-инжиниринг». Сегодня это одна из самых динамично развивающихся малых компаний в Санкт-Петербурге – всего лишь за три года объем НИОКР, выполняемых сотрудниками МИП, достиг 65 млн рублей, что, вообще говоря, превышает объемы НИОКР большинства университетских кафедр.
Подчеркну, так как это принципиально важно – результаты деятельности университетского инжинирингового центра и МИП в отчетах суммируются, возникает реальное взаимодействие университета и наукоемкого бизнеса, реально создаются высокопроизводительные рабочие места, главное – формируется экосистема инноваций. Теперь осталось только, чтобы Минобрнауки учитывало результаты деятельности университетских стартапов в отчетных университетских документах…
В связи с этим сошлюсь на впечатляющий опыт университетского мирового лидера, я имею ввиду Массачусетский технологический институт (MIT), так вот – объем всех наукоемких бизнесов, созданных MIT, примерно равен ВВП 17-й экономики мира! Это и есть ярчайший пример формирования экосистемы инноваций, в которой есть место и актуальным исследованиям, и технологическому предпринимательству, и малому наукоемкому бизнесу, и, конечно, тесному взаимодействию с высокотехнологичными корпорациями. Именно эта модель, объединяющая образование, исследования и разработки, технологическое предпринимательство, взята за основу при создании в феврале этого года в нашем университете Института передовых производственных технологий (ИППТ) на базе передового российского инжинирингового центра СПбПУ.
– Вы просто идеально вписались в заданный министерствами формат!
– Наверное, так можно сказать. Главное, что это правильные форматы, они реально эффективно работают на практике.
– Но возникает другой вопрос – столь ориентированные на бизнес старт-апы и спин-ауты не отвернутся от университета?
– Конечно, нет. Эффективное взаимодействие выгодно обеим сторонам, во всем мире ведущие университеты являются центром экосистемы инноваций, а малые предприятия должны играть роль технологических брокеров – профессиональных посредников между фундаментальной и прикладной наукой и высокотехнологичной промышленностью. Кроме того, сотрудники инжинирингового центра и МИП вовлечены в учебный процесс, выступают соруководителями бакалаврских работ и магистерских диссертаций. Именно они обеспечивают реализацию принципа – «подготовка инженера в процессе выполнения реальных НИОКР по заказам промышленности».
По сути это практико-ориентированный подход нового поколения: в процессе обучения преподаватель-практик-инженер и студенты старших курсов совместно решают актуальные научно-технические задачи по заказам промышленности, а не рассматривают кейсы из учебников… Обычно мы гостям показываем каталог магистерских диссертаций и бакалаврских работ, выполненных в лаборатории «Вычислительная механика» и Центре компьютерного инжиниринга за последние годы. В этом каталоге представлены десятки выпускных работ, каждая работа навеяна той или иной НИОКР для промышленности.
– Я этот каталог изучал и, не вдаваясь в подробности, готов подтвердить: в нем собраны конкретные научно-технические и промышленные задачи.
– Это отметили и министры, Мантуров и Ливанов, и такой апологет практико-ориентированного обучения, как президент-основатель и ректор Сколтеха Эдвард Кроули, который специально приезжал в наш инжиниринговый центр изучать опыт подготовки инженеров нового поколения, обладающих компетенциями мирового уровня. И если где-то на занятиях рассказывают, как надо взаимодействовать с мировыми компаниями, например, Boeing и BMW, то наши инженеры (они же преподаватели!) в 2006 году работали в дизайн-центре Boeing и участвовали в проектировании композитных структур Boeing 787 Dreamliner; именно наши российские инженеры обеспечивают пассивную безопасность для широкого ряда автомобилей BMW. Мы изнутри знаем проектирование, технологические и производственные процессы ведущих мировых фирм и в процессе обучения идем от промышленных задач-вызовов, опираясь на фундаментальную физико-математическую подготовку и передовые технологии мирового уровня. Мы уверены, что только так можно подготовить научно-техническую и инженерную элиту нации, или, как говорит ректор Политехнического университета Андрей Иванович Рудской, – «инженерный спецназ».
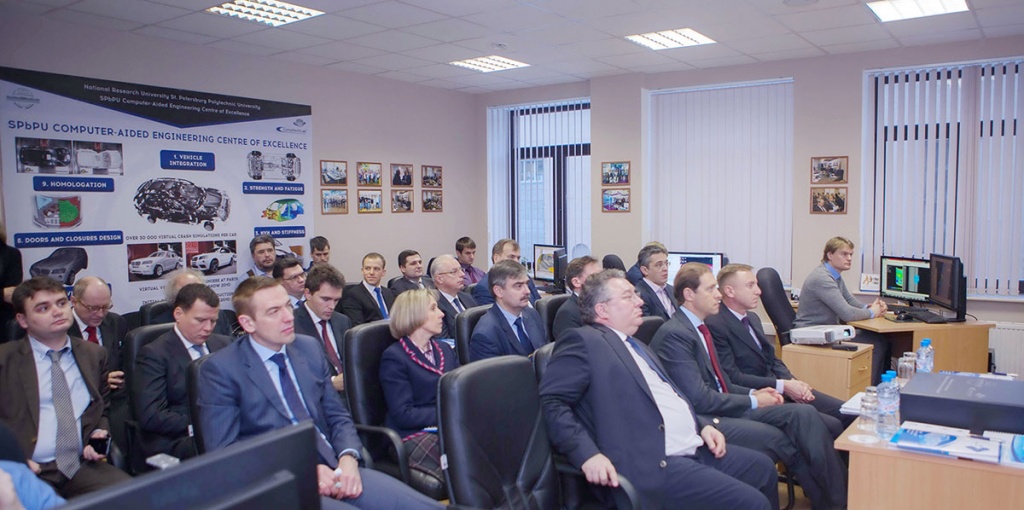
– До сих пор мы говорили о вашей кооперации с западными компаниями. Но импортозамещение, причем в условиях санкций – принципиально иная задача. С чего следует начинать ее решение?
– Ну, хотя бы с такой «маленькой» шпильки, весом около 10 кг. Почему эта шпилька – воплощение импортозамещения и глобальной конкурентоспособности? Потому что она с морской ледостойкой стационарной платформы «Приразломная», а только налоги от разработки Приразломного месторождения за весь период реализации проекта принесут в бюджет 650 млрд рублей. Кроме бурового комплекса, энергетических установок и т.д. на платформе есть подъемный кран, работающий, как и вся платформа, в условиях арктического шельфа, а шпильки крепят его опорно-поворотное устройство.
Выясняется, что практически 90% оборудования на платформе – импортное, из США и стран ЕС, изготовлено и обслуживается нашими зарубежными партнерами-заказчиками, для которых мы в разные годы выполняли много НИОКР. В прежние годы как рассуждали? «Нефть – дорогая, денег у нас много, мы все купим за рубежом». Соответственно, сервисные компании на вертолете привозили новые детали, оборудование, в частности, шпильки, и заменяли отработавший свой ресурс детали. В год таких деталей нужно более 20 000 (!).
В сегодняшних условиях санкционного давления традиционная схема уже не проходит, а делиться с Россией секретами проектирования и изготовления высокотехнологичного оборудования никто не собирается. Для его изготовления на российских предприятиях необходима РКД – рабочая конструкторская документация на все детали, машины и оборудование, а ее, документации, нет!
Вот мы и посоветовали Минпромторгу объявить среди инжиниринговых центров и компаний конкурс на создание в кратчайшие сроки, за свой счет, простейшей детали – шпильки. Чтобы не просто деньги всем раздать и выяснять через год, что и почему не получилось, а положить на стол ту самую импортную (!) шпильку и поставить задачу – через две недели положить рядом точно такую же, но уже российскую. Причем создать ее нужно при отсутствии какой-либо дополнительной информации, но если ты называешь себя специалистом, инженером – изготовь! Только, чтобы изготовить точно такую же шпильку, нужно было сначала разработать РКД….
– Пойди туда, не знаю куда, принеси то, не знаю что?
– «Куда» и «что» было в общих чертах понятно: нам дали отработавшую свой срок, со следами смазки шпильку и предложили сделать такую же. После первичного обследования (спектральный анализ химического состава материала шпильки, «оцифровка геометрии» путем лазерного сканирования и т.д.), мы, располагая уникальной базой данных о химических и физико-механических свойствах 240 000 материалов, составили «список номинантов»: 13 американских и европейских сталей, из которых она могла быть сделана. Детальное изучение химического состава позволило сделать окончательный выбор и консервативно, с запасом по прочности, найти российский аналог. Обращаемся на российские предприятия и опять слышим: давайте РКД, мы все изготовим. Но документации нет, страна же шпильки покупала, а не чертежи и технологии, соответственно, ее надо разработать. Для нас, специалистов высшей школы это был профессиональный вызов.
Принципиально важно, инжиниринговый центр Политехнического университета смог разработать не просто РКД для шпильки, а общий алгоритм действий для импортозамещения всей номенклатуры изделий из широкого спектра высокотехнологического оборудования, применяемого в промышленности.
Как люди осведомленные о реальном состоянии нашей промышленности, мы попытались разместить заказ на шпильку в десяти разных местах. Увы, многие из тех, кто обещал при наличии РКД изготовить деталь без проблем, оказались несостоятельны. Причины? У кого-то не нашлось нужного металла, кто-то не смог резьбу нарезать («резец не так пошел»). Крупные заводы даже браться не стали за изготовление «какой-то шпильки».
Эта работа, которую нужно было выполнить за несколько дней, показала, что и внутри вуза нужно убирать барьеры – структурные, междисциплинарные, зачастую – организационные, чтобы совместить знания и умения в одном месте, ведь исторически и фактически они оказались рассредоточеными по нескольким институтам и кафедрам. Именно инжиниринговый центр выполнил «сборку» всего жизненного цикла реинжиниринга простейшей детали, от спектрального анализа и разработки РКД до изготовления, термообработки и независимого контроля качества. В итоге за несколько дней мы сделали шпильку – абсолютный аналог той, что была доставлена с платформы «Приразломная».
– Тем самым вы замкнули разорванную инновационную цепочку между исследователями, проектировщиками и изготовителями. Но могут ли центры инжиниринга (в современном, широком его понимании, а не в привычном «монтаж и пусконаладка оборудования») обеспечить подобное технологическое партнерство в масштабах страны?
– Чтобы оценить картину в масштабах страны, отмечу, что только для платформы «Приразломная» в год необходимо 20-25 тысяч деталей, а с учетом ввода в эксплуатацию новых буровых скважин к 2020 году ежегодно будет нужно около 150 тысяч деталей. В расчете на отрасль, ежегодную емкость рынка можно оценить как 1,5 миллиона деталей. И это лишь один фрагмент проблемы импортозамещения, которая у всех сейчас на слуху.
Важно понимать, что в первые два года нам потребуются простейшие детали типа шпильки: уплотнения, кольца, шланги, манжеты, хомуты. Но затем потребуются капитальные запчасти – роторы, валы, рабочие колеса, электроприводы, насосы, компрессоры и другие агрегаты. В них происходят сложнейшие гидродинамические и тепловые процессы, а значит, они должны быть прочными, надежными, долговечными, и, наконец, ремонтопригодными.
Поэтому дело отнюдь не только в шпильках. Речь о высокотехнологичном оборудовании, которое мировые лидеры разрабатывали и совершенствовали годами в ходе многолетней эксплуатации. Более того, сложность конструкций и внутреннего их устройства такова, что без методов компьютерной томографии и интроскопии не обойтись. То есть за короткий срок мы должны восстановить весь жизненный цикл проектирования и производства высокотехнологичного оборудования. А решив задачу импортозамещения, «подпрыгнув до мирового уровня», вплотную заняться другой, более важной проблемой – экспортоориентированного импортоопережения. И так по всему спектру продукции для нефтегазодобывающего комплекса, а также для других отраслей промышленности.
Вообще эта история убедительно показывает, что в отечественной промышленности не хватает интеллектуальных ресурсов и, главное, практики быстрого формирования проектных консорциумов для решения задач-вызовов с участием ограниченного количества специалистов, обладающих компетенциями мирового уровня, включая университетских. В нашем случае, это проектные консорциумы, работающие по заказам крупнейших нефтегазовых компаний страны и выполняющие роль центров обратного (реверсивного) инжиниринга, центров компетенции. Их зона ответственности – изучение прототипа, проектирование, разработка РКД и, возможно, выпуск опытного образца, мелкой серии, а также – независимая экспертиза.
– Неужели мы настолько отстали от мирового уровня, что обречены копировать и догонять?
– Вспомните, весь мир показывал пальцем на Китай – они, мол, всегда, всё и у всех копируют. А они «докопировались» до того, что создали вторую по объему экономику в мире. Это целенаправленный подход, учитывающий особенности нации, который полностью себя оправдал. Мы же любим начинать с нуля, мы должны быть первыми во всем, начиная с фундаментальных основ и частенько забываем о том, что временные циклы создания новой продукции стремительно сокращаются, конкуренция смещается в сторону создания в кратчайшие сроки глобально конкурентоспособной продукции нового поколения. Такую продукцию можно создавать только с применением новых материалов, на основе передовых технологий проектирования, компьютерного инжиниринга, многокритериальной, многопараметрической и топологической оптимизации, а также передовых производственных технологий: от многофункциональных обрабатывающих многоосевых фрезерно-токарных центров до современных установок аддитивного производства.
Звучит, может быть, сложновато, но лишь конвергенция и синергия технологий компьютерного и суперкомпьютерного инжиниринга, компьютерного проектирования на основе математического моделирования, принципов бионического дизайна и применения технологий оптимизации совместно с аддитивными технологиями позволит создавать best-in-class оптимизированные изделия и конструкции.
– Похоже, отвечая на мой вопрос, Вы сформулировали ближайшие цели для инжинирингового центра и Института передовых производственных технологий?
– Да, именно эти задачи мы ставим и будем решать в Санкт-Петербургском политехническом университете Петра Великого, понимая, что наша основная задача – подготовка специалистов для будущей инновационной экономики России, владеющих наукоемкими технологиями и обладающих компетенциями мирового уровня. А этого уровня можно достичь, работая на регулярной основе с ведущими отечественными и зарубежными высокотехнологичными компаниями.